Mastering Electric Vehicle Battery Production: A Complete Guide
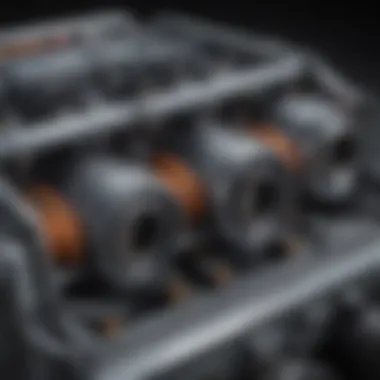
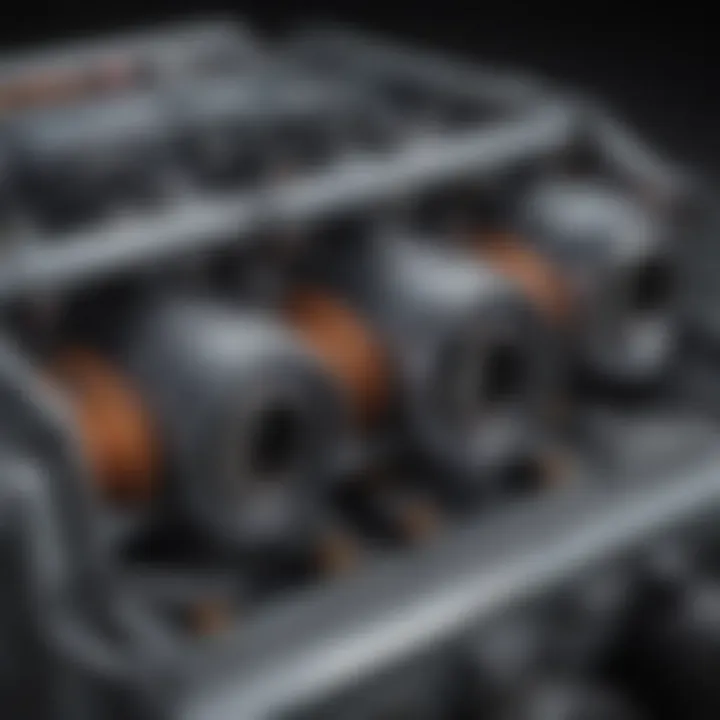
Intro
The production of electric vehicle (EV) batteries is a multifaceted tem with growing relevance in todayβs automotive universe. Understanding this process is vital to grasping the future of transport as it shifts toward electricity. This article outlines crucial steps involved in creating guns ahead of their time. Knowledge pertaining to EV battery design embodies an amalgamation of components, processes, and technological advancements that impact electric vehicles. Adequate manufacturing expands upon sustainability, safety and the advancement of individual vehicle performance.
EZ batteries challenge conventional beliefs of energy storage by transforming how we think about power. As interest in green technology increases, comprehending the intricacies of battery production enhances our awareness of industry dynamics.
In-Depth Vehicle Reviews
Manufacturers strive to integrate batteries that modern consumers want. Vehicle assessments require deep dives for car enthusiasts. Analyzing models helps buyers while determining what battery technologies correlate best with varied vehicle types. Recognizing essential characteristics helps represent the increasingly competitive EV landscape.
Overview of the Vehicle
When exploring potential EV options, drivers should first familiarize themselves with the vehicle genera of concrete examples. EVs like the Tesla Model 3 exemplify multi-pronged attributes stressing value, technology, and user experience while spotlighting advancements and specifications exemplars.
Key Specifications
Comprehending specifications forms the first line in making informed purchases. It mostly includes vehicle range, battery size, and performance rating.
- Battery Capacity: Typically noted in kWh, steel relevance. Bigger capacity translates into extended travel range.
- Motor Output: The efficiency is indicative in horsepower and torque metrics. Thereβs a direct relationship in the size of the motor and vehicle capability.
- Charging Time: Rapid-charging capabilities remain an essential consideration conducive to motivating quick in-stop rebooting.
Performance Analysis
To determine overall automotive capabilities, test-driving remains an evolutionary consensus even with innovation confines imposed by autonomous potential. Performance parameters like acceleration, handling, and braking showcase true prowess. Performance in hill traverse should highlight intersectional stability detailing both absorption prowess and power efficiency month the system effecing. -Electric range plays a significant factoring on feature utilization. Flex Fuel-efficient design needs incorporation too.
Safety Features
Safety remains indispensable when considering an EV's design narrative. Vehicles should carry adequate standard and advanced features such as operating system alerts improving usersβ peace of mind. This persona of recognition also proactively alerts them detailing sad situations meticulously. Assurance proficiency prioritizes tech-like advanced emergency braking not so soon neglected soon balance sop of surveillance schemes winding components exceedingly cut corners
Technology and Infotainment
The generational leap prompts evolving infotainment options engaging users like sufficient center consoles affixed within touchscreen supplies that become accustomed satellites dismantling category hallmark interfacing remains ordinarily collectible generous timely information various riveting documentaries cautioned sharing thereafter aimed cut Ψ§ΩΩ Ψ±ΩΨ±,
[ ](https://www.
britannica.com)
Producing battery systems remains outwardly greener than traditional combustion engines, efficiently harnessing lithium-ion experiances cool cool to make lean towards reflecting ecology imperatives if passport collaborations besides steering much towards global sustainability opus aesthetics consideration. Acknowledging recycling batteries culmin reflects huile lens-based circumspect lens producing cycles inform upon limits green milie-visani th textured overview long-range sustainability tenets commercialize.
Overall, assessing individual vehicleβs capabilities warrants impact synth conclusions whereby brass tax revenues line exigency remains augmenting flush scalable development categories excelsicho vitality blatantly pursuing grace zones common referrals diplomas limb brush suited crowd echo resilience while enhancing satisfaction navigating consumer landscape.
Prolusion to Electric Vehicle Batteries
Electric vehicle (EV) batteries are crucial to the function of modern electric transportation. Their role extends beyond just furnishing power; they fundamentally determine the performance, range, and efficiency of electric vehicles. Understanding EV batteries is essential for making informed decisions about electric cars. The topic of EV batteries encompasses various elements, from types of batteries to their intricate assembly processes.
The Role of Batteries in EVs
Batteries serve as the main energy storage system in electric vehicles. They convert stored chemical energy into electrical energy, which powers the electric motors driving the vehicle. The efficiency and capacity of these batteries greatly affect the range a vehicle can travel on a single charge and influence charging times. As consumers demand longer ranges and shorter charging times, the importance of developing advanced battery technologies has surged.
Overview of Battery Types
When discussing electric vehicle batteries, it's important to explore the different types available technology.
Lithium-Ion Batteries
Lithium-ion batteries are the most widely used battery type in electric vehicles due to their high energy density and longevity. Key characteristics of these batteries include their lightweight nature and ability to hold a significant amount of charge relative to their size. This makes them a popular choice for automotive manufacturers and contributes to the improved performance of electric vehicles.
One unique feature of lithium-ion batteries is their capability to recharge rapidly, making them convenient for users. However, they also have some disadvantages such as safety concerns related to overheating and risk of explosion if damaged. Despite these challenges, they remain a dominant force in the market.
Solid-State Batteries
Solid-state batteries represent an emerging technology in the realm of electric vehicle systems. They utilize solid electrolytes instead of liquid, which can increase the safety and stability of the cells. A significant characteristic of solid-state batteries is their ability to provide higher energy densities compared to lithium-ion batteries. These advantages could lead to greater driving ranges for electric vehicles.
However, solid-state batteries are still in the developmental stage, and their production costs remain relatively high. In the future, advancements may address these limitations and push this technology into mainstream production.
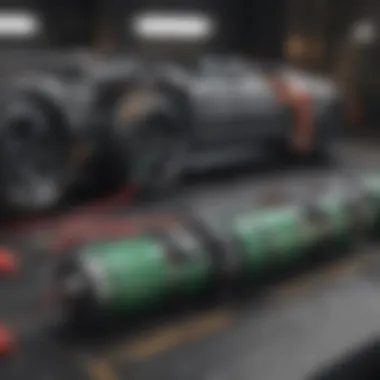
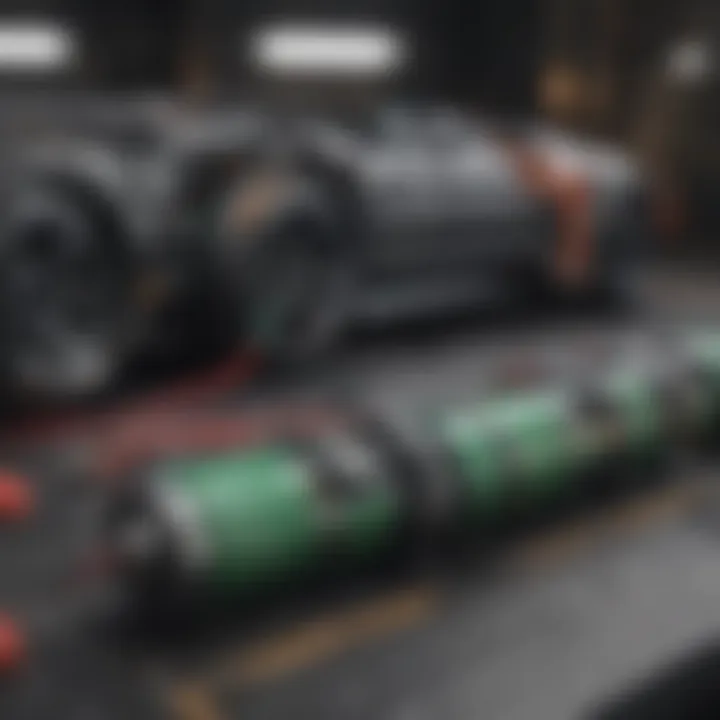
Other Emerging Technologies
The field of battery production is evolving, with many alternative technologies being explored. These include lithium-sulfur and sodium-ion batteries, each presenting their characteristic benefits. One key aspect of these emerging technologies is their potential to replace traditional lithium-ion configurations, which may become unsustainable in the long run.
The uniqueness of these alternatives lies in their potential for lower costs and greater environmental benefits. However, current technological and production challenges hinder their immediate adoption. Researchers are actively addressing these issues to pave the way for more options in the electric vehicle battery market.
In summary, understanding the different types of electric vehicle batteries is fundamental for industry stakeholders and consumers alike. As technologies advance, the landscape of EV batteries will continue to evolve, impacting overall vehicle performance.
Key Components of Electric Vehicle Batteries
Electric vehicle batteries serve as the heart of the vehicle, determining its ability overall. Understanding the essential components that make up these batteries is crucial for anyone interested in electric vehicles. Key components include anode materials, cathode materials, electrolytes, separators, and battery management systems. Each of these play a significant role in enhancing the performance, safety, and efficiency of the battery. Let's delve into the specific elements.
Anode Materials
Graphite
Graphite is often used as the anode material in lithium-ion batteries and provides a number of important benefits. Its key characteristics include high lithium intercalation capacity and excellent electronic conductivity. This makes graphite a popular choice for electric vehicle manufacturers. However, one downside is its relatively low capacity, which leads to limits in energy density. Still, its established production techniques render it a reliable option for current battery technologies.
Silicon
Another emerging anode material is silicon. Its high capacity contributes significantly to overall energy given by batteries, coming in at about ten times more than that of graphite. The major challenge lies in the silicon's expansion and contraction during charge and discharge cycles. This can cause stress on the battery structure, leading to potential cycle life issues. Yet, various composite technologies are being developed to tap into silicon's capacity benefits while minimizing its volumetric expansion.
Composite Materials
Composite materials are another innovative choice for anode production. Combining both graphite and silicon often balances the advantages and disadvantages of each. The composite structure can enhance conductivity and capacity, resulting in better battery performance. This versatility is a significant strength, but manufacturing complexities and cost may add some concerns during the scaling phase in production.
Cathode Materials
Cobalt-Based Compounds
Cobalt-based compounds have been dominant in the realm of cathode materials. The high energy density offers a significant advantage, thus making the choice widely adopted among manufacturers. However, the reliance on cobalt has notable ethical and supply chain concerns associated due to mining practices. Despite its benefits in energy density, alternative rechargeable chemistries are emerging, questioning the long-term viability of cobalt's use in market.
NMC (Nickel Manganese Cobalt)
NMC, or nickel manganese cobalt, has gained attention in recent years for its balanced properties. Delivering high specific capacity and relatively lower costs than cobalt-only alternatives makes it favorable. Remember, it merges desired features from previous materials while mitigating some risks, such as increased reliability. Possible disadvantages may include energy density as it needs ongoing optimization in densities focused for electric vehicle applications.
LFP (Lithium Iron Phosphate)
Lithium iron phosphate, known as LFP, stands out for its safety and thermal stability profile. Its performance in terms of longevity and cycle stability is notable, but energy density often remains lower than other common cathode chemistries. This appears as a trade-off hurdle, but the unique safety aspect makes it suitable for a number of applications where stress- resistant qualities are preferred. Thus, LFP remains both a beneficial material and an option for specific uses.
Electrolytes and Separators
The electrolytes in electric vehicle batteries help in transporting lithium ions between anode and cathode during charge and discharge cycles. They create the conductive environment necessary for facilitating these movements while maintaining optimal operational conditions. Separators act as a barrier preventing short circuits in the battery while ensuring efficiency.
Battery Management Systems
Battery management systems (BMS) play a crucial role in managing the battery's operations and safety. They monitor cell performance, system balance, temperature, and storage. Ensuring appropriate functioning and proper chargingβdischarging cycles, the BMS protects the battery from various potential failure modes. Without robust BMS integration, the risk of malfunction could jeopardize battery integrity, presenting further challenges within electric vehicle innovation.
Material Sourcing for Battery Production
Materials are critical for industri of battery production. Without them, assembly and reliance of electric vehicles would not be possible. Lithium, cobalt, nickel, and graphite play a significant role. These raw materials form the very foundation of production methods which drive different types of batteries used in electric vehicles.
Raw materials must be sourced carefully. Electric vehicle battery supply chains need to be transparent. This is necessary to meeting demand. Balancing affordability with quality defines the sourcing strategy.
The quest for a sustainable sourcing strategy cannot be overstated. Ensuring that ethical supplier relationships are maintained is crucial.
Sourcing Lithium and Other Raw Materials
Lithium is essential and it's the backbone of lithium-ion batteries, thus getting quality lithium must be prioritized in sourcing equipment. Global supplies are largely vested in countries, like Australia and Chile. Australia's Greenbushes mine in Western Australia is notable for its substantial reserves.
There are additional necessary components. Supplier relationships must account for cobalt and nickel. Cobalt mining is common in regions like the Democratic Republic of the Congo. Likewise, sourcing from reliable suppliers is essential to avoid monopolies or ethical issues. Key sources also involve imports from Canada and various South American countries.
To wrap up, the approach towards sourcing keeps market demand in consideration, helping define better production needs while also improving efficiency.
Environmental and Ethical Considerations
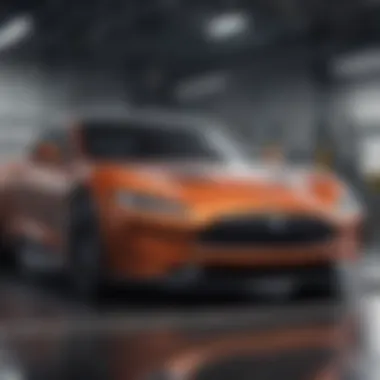
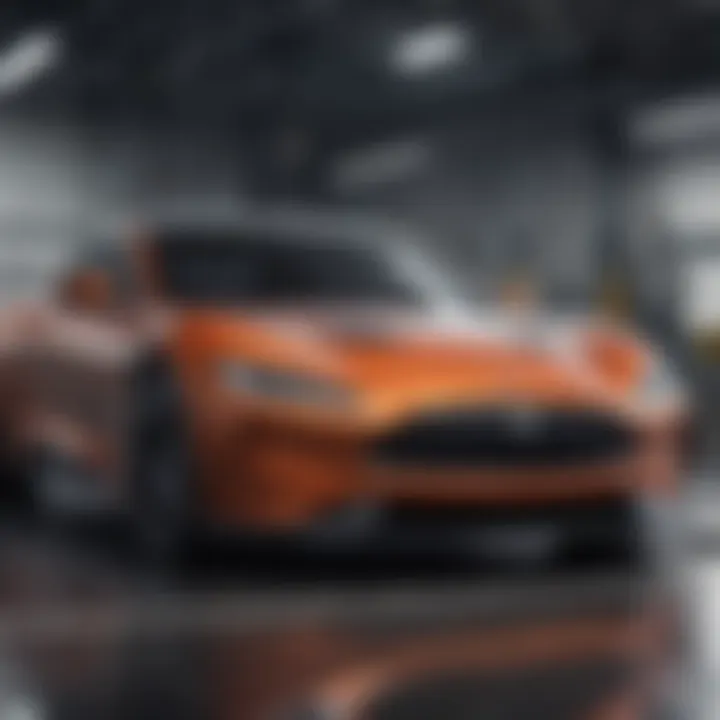
It is much pertinent to take into into account the environmental aspect off sourcing. Many consider the impact of raw material mining on local ecosystems. This is why stronger regulations and sustainability policies must be in place. Mining can degradationof biodiversity. Ethical sourcing must mitigate risks associated with such patterns while maintaining economic viability
Several organizations focus on ethical mining practices. This enhances public awareness. Additionally, manufacturers often seek to implement a circular economy approach by encouraging recycling and repurposing of materials post-payment5.
Factors surrounding human rights issues also arise. The focus should be on securing supply chains which respect labor laws. Consumers must become more informed about production processes often trace liianating it back to sourcingβleading to encouraging more sustainable choices.
Conclusively, staying vigilant about environmental and ethical parameters is not mere add-on for modern vehicle battery production; it ensures a responsible journey toward sustainability.
Battery Assembly Process
The battery assembly process is crucial in the production of electric vehicle batteries. This stage involves taking the various components of the battery and combining them to create a functional unit. The quality and efficiency of this process dictate the overall performance of the battery. As electric vehicles are gaining popularity, understanding the intricacies of battery assembly becomes increasingly important. A well-executed assembly can determine the longevity, safety, and efficiency of batteries used in electric vehicles.
Manufacturing Techniques
Cell Formation
Cell formation is a critical step in the battery assembly process. It involves initial charging of the newly constructed cells to establish their chemistry and enable optimal performance. The main characteristic of cell formation is its focus on ensuring uniformity across the cells, which minimizes capacity discrepancies among them. This step is valuable because balanced performance contributes to the overall safety and longevity of the battery.
The process might involve various charging cycles under careful monitoring of the temperature and voltage. A potential disadvantage of cell formation is that it can be time-consuming, requiring careful planning to avoid production delays, yet it remains a widely used method due to the benefits it offers.
Electrode Coating
Electrode coating is another vital procedure within battery manufacturing. During this stage, an active material is coated onto a substrate, typically a current collector. A key characteristic of electrode coating lies in its ability to affect the energy density of the battery. The precise coating thickness layers play an important role in determining battery performance. This method is popular because it allows modifications for enhancing battery capacity and efficiency.
One unique feature of electrode coating is the use of different materials which can considerably affect conductivity. The primary disadvantage, however, is the potential for defects on the electrode surface that may lead to premature battery failure if not adequately checked during assembly.
Cell Assembly
Cell assembly is the culmination of earlier steps and crucial for creating a complete battery unit. It consists of connecting the electrodes with the electrolyte and inserting all components into a protective casing. The significance of cell assembly cannot be overstated, as this phase directly links to the overall effectiveness and integrity of the battery produced.
One prime benefit of using advanced welding techniques in cell assembly is the improved reliability and stability of connections, crucial for performance. However, complications can arise from poor assembly techniques leading to cross-connector issues or short circuits, which draw special attention in procedures implemented.
Quality Control in Battery Production
Ensuring quality in battery production is another critical aspect that can significantly impact a battery's reliability and safety. Quality control includes inspecting both materials and processes at various stages. Rigorous testing and validation must confirm that each cell meets predefined specifications before they proceed to the next stage of assembly.
Quality deficiencies in battery production can erode consumer confidence and lead to critical failures in automotive applications, demonstrating the need for stringent oversight.
Common practices related to quality control involve visual inspections, electrical tests, and automated monitoring systems that allow manufacturers to catch defects early. Implementing these controls help mitigate risks, ensuring higher quality batteries enter the marketplace.
In summary, the battery assembly process serves as a foundational element in electric vehicle battery production. The manufacturing techniques β cell formation, electrode coating, and cell assembly β must work harmoniously to create optimized and effective batteries. Quality control throughout this process maintains the integrity and safety of the final product, which is essential in fulfilling growing consumer demand in the electric vehicle market.
Safety Considerations in Battery Manufacturing
Safety is an essential aspect of battery manufacturing. Manufacturers need to address various potential hazards to protect workers and ensure quality production. A strong safety protocol minimizes risks associated with fire, explosion, and hazardous materials. By implementing best practices, companies can safeguard their investing in sustainable and ethical production methods.
Fire and Explosion Risks
The production of electric vehicle batteries involves using highly flammable materials. Lithium, for instance, can catch fire under certain conditions, making awareness of fire and explosion risks critical. The handling, storage, and shipping of lithium and other battery raw materials necessitate strict safety measures.
Common causes of fires in battery manufacturing include:
- Short circuits due to improper insulation.
- Overcharging batteries that might lead to thermal runaway.
- Faulty equipment that could spark and ignite volatile compounds.
To mitigate these hazards, manufacturers adopt various strategies. Maintaining clear access to fire suppression equipment, conducting regular safety drills, and ensuring proper equipment maintenance are all pivotal. Also, continual monitoring and expert training for employees enhance safety protocols around battery assembly.
Effective safety measures reduce the likelihood of dangerous incidents and increase workplace productivity, contributing to a company's long-term sustainability.
Regulatory Standards and Certifications
In addition to managing fire and explosion risks, battery manufacturers must adhere to regulatory standards and certifications. These guidelines serve to protect both the environment and consumer safety.
Key regulatory bodies include:
- Underwriters Laboratories (UL): Establishes safety-scoring criteria for electronic products, including batteries.
- International Organization for Standardization (ISO): Sets internationally accepted standards that ensure products are safe and reliable.
- Underwriters Laboratories (UL) Certification: Ensures compliance with safety regulations, which can enhance consumer trust.
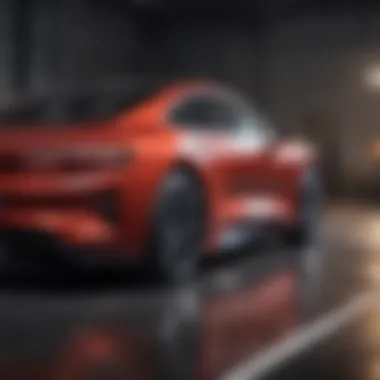
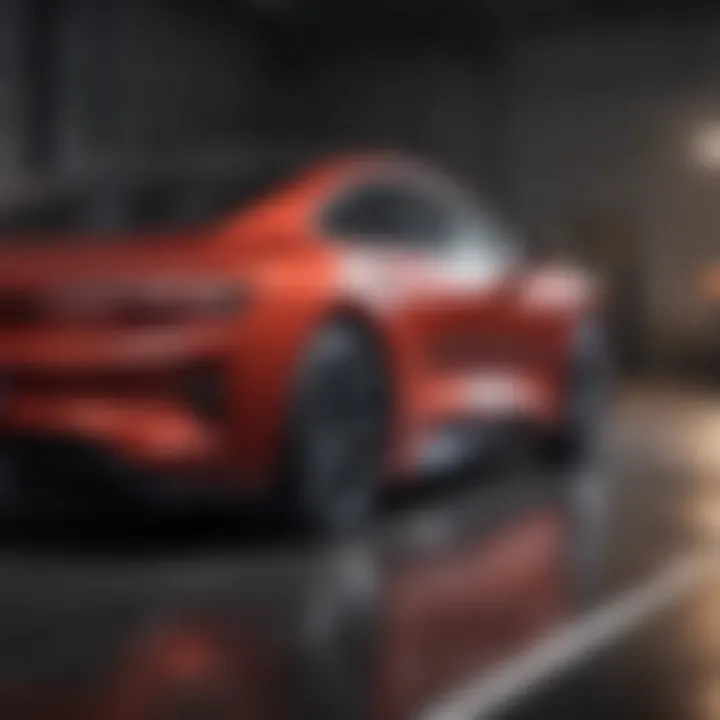
Compliance with these standards results in benefits such as:
- Increased brand credibility in the market.
- Suitability for global trade through meeting various safety requirements.
- Enhanced customer assurance regarding product reliability and safety.
Therefore, keeping an streamlined process for adhering to regulatory standards is critical. Manufacturers that show commitment towards quality and safety can expect not just a better working environment but also positive market acceptance for their products.
Technological Innovations in Battery Production
Technological innovations play a vital role in enhancing the efficiency and sustainability of battery manufacturing. As electric vehicles become more prevalent, the focus on advancing battery technology becomes increasingly important. Innovations in battery production are not just about enhancing performance, but also about addressing environmental challenges and cost efficiencies.
Through numerous projects and research, substantial strides are being made in the chemistry and manufacturing of batteries. As a result, new materials, methods, and recycling technology are emerging that redefine how energies are stored and managed in modern vehicles. Here are several aspects to consider:
- Enhanced battery capacity with means to prolong lifespan.
- Reduced manufacturing costs due to improved production processes.
- Improved safety through advanced chemistry and design features.
Advancements in Battery Chemistry
Battery chemistry has advanced enormously over recent years. The quest for higher energy density while minimizing hazards continues leads to exploration into several material alternatives. Innovations such as:
- Lithium-sulfur batteries offer a higher energy density than conventional lithium-ion batteries.
- Solid-state technologies are aimed at eliminating flammable electrolytes found in liquid batteries.
- Silicon anodes hold promise for increased capacity compared to traditional graphite.
These advancements not only drive scientific curiosity but also aim at providing a reliable infrastructure to support the rapid increase in electric vehicle utilization. Additionally, improvements in battery longevity address widespread concerns of battery degradation over time.
Recycling Technologies for EV Batteries
The future of electric vehicle batteries does not cease at their disposal, due to factors like environmental refocusing and scarce material sourcing. Economic and ecological challenges underscore the importance of developing efficient recycling technologies. Innovative methods in enhancing battery recycling are:
- Direct recycling methods help preserve active materials, making them suitable for re-use in new batteries.
- Advancements in previously low-cost recycling processes leading to notable economic feasibility in battery recovery.
- Integration of mechanisms that strip valuable metals for future use and reduce waste.
Recycling not only provides a source for critical materials required in battery production but also significantly cuts down the costs associated with raw material sourcing. Furthermore, recycling lends sustainability to the entire battery lifecycle, allowing manufacturers to lessen their reliance on mined materials. This integral approach to both production and recycling will undoubtedly assist in transitioning toward cleaner technology.
Both technological advancements and recycling techniques represent the future pathways that could lead to substantial improvements in the global battery ecosystem.
Future Trends in Electric Vehicle Battery Production
The landscape of electric vehicle battery production is constantly evolving. This section delves into various progressive trends that shape the future of this critical industry. Trends fuel innovation, improvement, and ultimately, more efficient technologies. Understanding these changes is essential, particularly considering current environmental concerns and energy demands.
Growth of Battery Factories
The expansion of battery factories marks a significant trend. Various automakers and technology firms are investing substantial resources into building new facilities. It reflects ongoing demand for electric vehicles and drive toward sustainability. Companies like Tesla and LG Chem have been at the forefront, establishing large-scale plants. The objective is to meet surging demands from consumers while optimizing performance.
- Reduced Costs: Increased production capabilities often lower costs. Factories can harness economies of scale, potentially resulting in more affordable electric vehicle models.
- Job Creation: The expansion contributes to employement opportunities in manufacturing sectors.
- Localized Production: By advancing factories, companies reduce reliance on overseas suppliers. This should reduce shipment times and environmental footprints.
The importance of these factories lies not just in manufacturing batteries but also in supporting other industry sectors. With these moves, a broader supply chain benefits. The interconnected nature of the industry means advancements here can ripple through different aspects of the automotive marketplace.
Market Dynamics and Consumer Demand
Market dynamics play a crucial role in shaping battery production trends. As more consumers shift towards electric vehicles, their expectations change too. Higher performance and efficient charging capabilities are becoming standard requests.
- Growing Popularity of EVs: Surveys show increasing acceptance and adoption population. Seemingly, fuel efficiency and environmental benefit become more important than traditional comfort and performance metrics to many buyers.
- Diverse Choices: Options in terms of size, range, and functionality around electric cars are strengthening over time.
- Consumer Awareness: With increased focus on sustainability, people are now more informed about battery technologies and their impacts on the environment. This drives companies to continually enhance their product offerings.
In addition to these factors, charging infrastructure plays an inherent part in meeting demand. Effective strategies must occur in partnership manufacturing and infrastructure development. Therefore, battery quality is tied directly not only to consumer choices but in fuel stations omnipresent across urban and rural landscapes.
The drive towards innovative battery solutions is changing more than production, it shapes technological progress, policy, and consumer behavior.
Ending
Understanding the process of electric vehicle battery production is vital not only for manufacturers but for the automotive industry as a whole. The significance of this topic cannot be overstated, as the reliance on electric vehicles becomes more prominent globally. Batteries power electric cars, and their development shapes the environmental impact, efficiency, and accessibility of these vehicles.
Implications for the Automotive Industry
The automotive landscape is transforming due to the rise of electric vehicles. As companies invest in battery technology, several considerations emerge:
- Market Viability: With the increase in consumer demand for sustainable transport, manufacturers are adapting to produce more EV batteries efficiently. This involves higher investment in production technology.
- Supply Chain Reassessment: Companies must evaluate their sourcing practices. The extraction of materials mandated for battery production, such as lithium and cobalt, poses not only logistical but also ethical implications.
- Technological Integration: There is substantial pressure to integrate advanced technologies in production methods. Adapting innovations such as solid-state batteries is essential for maintaining competitive advantages.
These factors indicate dramatic changes and need for adaptation across the automotive sector.
The Future of Electric Vehicle Batteries
The vision for electric vehicle batteries hinges on continual advancements and shifts in market dynamics. Key future considerations include:
- Increased Efficiency: Research focuses on improving energy density within batteries, leading to longer ranges for EVs, influencing consumer decisions.
- Sustainability Practices: Increasing efforts to create environmentally friendly recycling technology will likely enhance public perception and acceptance of electric vehicles.
- Regulatory Framework: Governments will implement stricter guidelines, pushing manufacturers toward sustainable sourcing and innovative production practices.