The Intricate Process of Assembling a Honda Vehicle
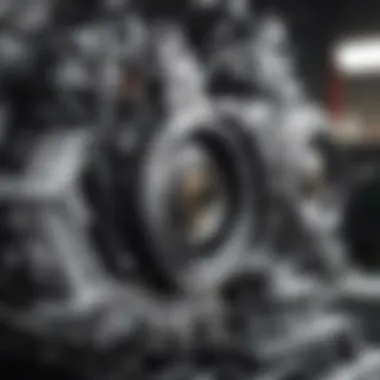
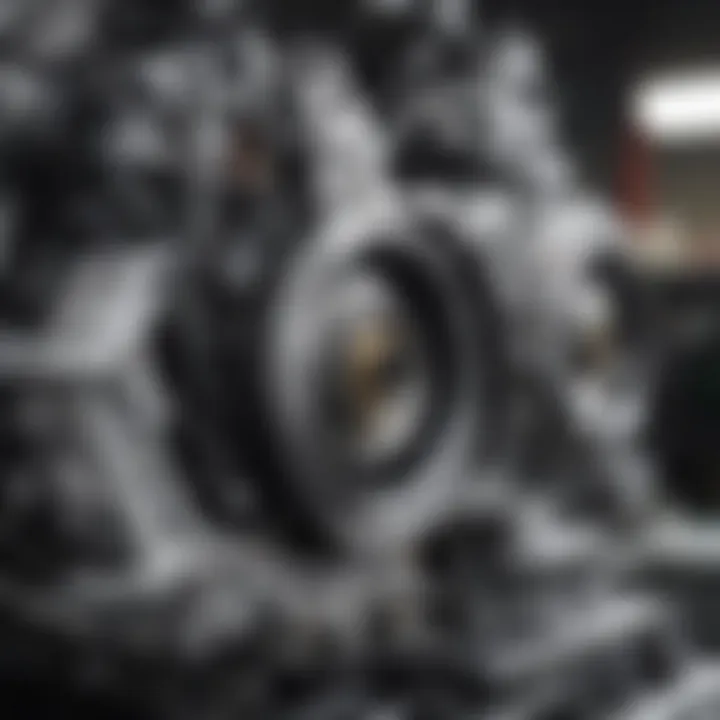
Intro
Assembling a vehicle is not just about putting parts together. It involves a complex blend of design, technology, labor, and quality control. In the automotive industry, Honda is recognized as a leader in these practices. For car enthusiasts and first-time buyers alike, understanding the process can illuminate how Honda maintains its standard of reliability and innovation. This guide presents a thorough breakdown of each stage involved in assembling a Honda vehicle, detailing the methodologies, technologies used, and key considerations that influence production decisions.
In-Depth Vehicle Reviews
Overview of the Vehicle
Honda vehicles come in various models that cater to different market segments. From compact cars like the Honda Civic to spacious SUVs like the Honda CR-V, each model offers a unique combination of features and specifications.
Key Specifications
When assessing a Honda vehicle, specifications play a critical role. For instance, the Honda Accord boasts a 1.5-liter turbocharged engine with a smooth CVT transmission, delivering a balance of performance and comfort. Fuel economy is another area where Honda excels, often achieving over 30 miles per gallon across many models.
Performance Analysis
Honda cars are engineered for a solid driving experience. They combine dependable powertrains with responsive steering systems. Whether on highways or city streets, Honda vehicles deliver a smooth ride, largely due to meticulous assembly processes that ensure precise tolerances.
Safety Features
Safety is paramount in any automotive production. Honda vehicles are equipped with advanced safety technologies such as the Honda Sensing Suite, which includes adaptive cruise control, lane-keeping assist, and collision mitigation braking. These features not only enhance driver visibility but also boost overall safety ratings in crash tests.
Technology and Infotainment
Modern Honda vehicles are equipped with cutting-edge infotainment systems. Features typically include touchscreen interfaces that integrate Apple CarPlay and Android Auto. This technology allows drivers to stay connected while prioritizing safety through hands-free operations.
Fuel Efficiency and Sustainability
As environmental concerns grow, so does the automotive industry's push towards sustainability. Honda continues to enhance fuel economy through hybrid options like the Honda Insight, which provides exceptional mileage along with reduced emissions. This commitment meshes well with current market trends favoring eco-friendly vehicles.
Understanding the nuances of technology and performance in Honda vehicles is essential for informed decisions, especially for potential buyers.
Maintenance and Ownership Costs
Overview of Regular Maintenance Needs
Like any vehicle, Honda models require routine maintenance, including oil changes and brake inspections. Regular checks help maintain performance and longevity.
Long-Term Ownership Costs
Honda vehicles tend to have lower ownership costs compared to competitors. Generally, part replacement and services come at reasonable prices, which is appealing for long-term users.
Tips for Reducing Maintenance Expenses
To minimize expenses, timely services and understanding warranty options are essential. Engaging with local third-party services sometimes saves money versus dealership prices.
Comparison of Warranty Options
Honda offers competitive warranties that generally include limited powertrain and overall vehicle coverage. Knowing these details can aid in confidence during and after purchasing.
Real Owner Experiences and Cost Experiences
Online forums like reddit.com provide authentic insights from Honda owners. Assessing these experiences can inform prospective buyers about long-term reliability.
Final Thoughts
This detailed examination illustrates why Honda maintains a strong reputation in the automotive sector. From the meticulous assembly process to dedicated warranties, factors influence overall vehicle performance and value. Car buyers can benefit from this knowledge by gravitating towards Honda models, known for reliability and innovation.
Intro to Honda Manufacturing
The process of assembling a Honda goes beyond just nuts and bolts; it encapsulates a complex series of practices that reflect meticulous engineering, innovation, and an unwavering focus on quality. Understanding Chevrolet's manufacturing processes provides insight not only into how these cars are built, but also why they enjoy esteemed reputations worldwide. In this section, we will examine the historical context and current market position of Honda.
Historical Context
Honda was founded in 1948 in Japan by Soichiro Honda and has steadily evolved into one of the worldรขโฌโขs leading automobile manufacturers. Initially starting as a motorcycle producer, Honda expanded its product line into automobiles in the 1960s with models such as the T360 truck and S500 sports car. It was not until the late 1970s that they started capitalizing on international markets with the introduction of the Honda Accord. Their success in this regard can be attributed to a profound commitment to quality and innovation, which helped them establish a foothold in the competitive automotive landscape.
Following years of continuous improvement and adaptation, Honda has embraced multiple technology shifts and regulatory changes to remain relevant, including the acceptance of eco-friendly automotive practices. Honda's historical significance is a narrative of resilience, flexibility, and a forward-thinking approach to manufacturing, which continues to inform its practices in the present day.
Current Market Position
As of 2023, Honda ranks among the top automobile manufacturers globally. Its market share reflects strong performance not only in Asia but also in North America and Europe. The company produces a diverse spectrum of vehicles, from compact sedans like the Civic to midsize SUVs such as the CR-V. Their dedication to quality and advancements in automotive technology contribute to strong brand loyalty and an esteemed reputation among consumers. Honda's continued effort to invest in hybrid and electric technologies displays their commitment to sustainability and innovation as they navigate ever-evolving market dynamics.
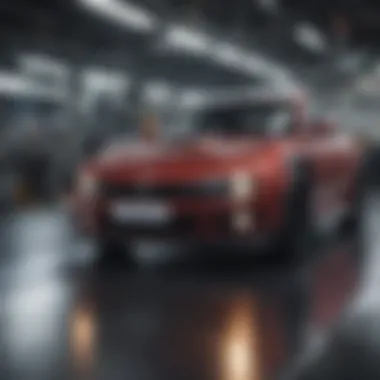
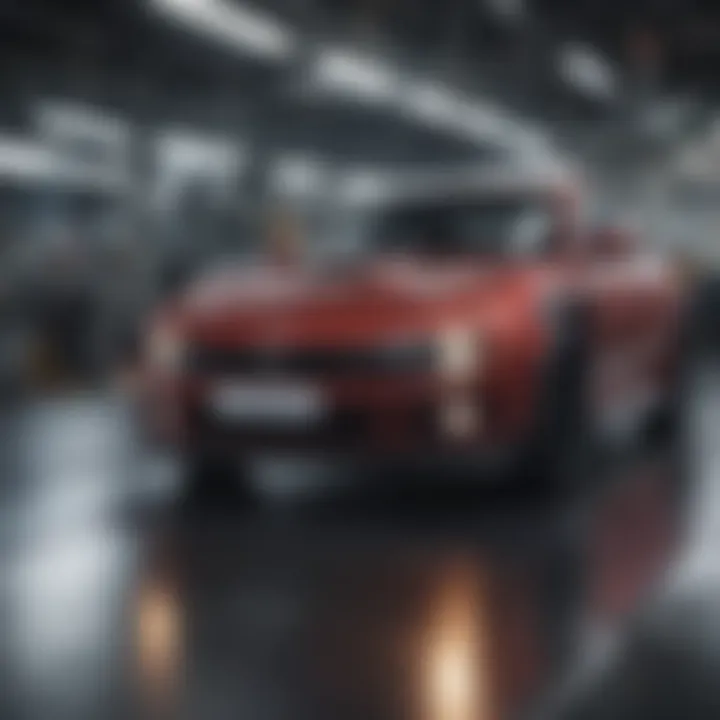
Honda now commands a significant influence in the competitive landscape, emphasizing reliability while striving for eco-conscious production methods during off sets like electrification of vehicles.
Honda's storied history and adaptive strategy are essential for understanding their resilience in changing market conditions and consumer expectations.
Design Phase
The design phase is a critical stage in the assembly of Honda vehicles. This is where automotive concepts transform into tangible products. Important choices made during this process not only determinate the functionality of the vehicle but also its aesthetics and performance.
Concept Development
Concept development serves as the foundation off the design phase. Here, engineers and designers collaborate to generate innovative ideas that align with market demand and Hondaโs brand identity. Focus group surveys and market analysis play an essential role in guiding decisions.
Factors considered in this stage include:
- Customer Expectations: Deep understanding of what potential car owners want, which could be fuel efficiency or advanced technology features.
- Regulatory Standards: Vehicles must adhere to environmental and safety regulations, which impact initial concepts.
- Feasibility Assessments: Projects are evaluated against resource availability like materials and budget constraints.
Through this iterative process, a preliminary vision of the vehicle begins to take shape. This step aids not only in creating designs that consumers desire but also decreasing later-stage modifications that can cost more in time and resources.
Prototyping
Prototyping follows concept development, allowing Honda to test and validate their ideas. This stage is vital as it bridges ideas with reality. Honda engages its strong research and development teams to create physical models, whether they be scaled versions or full-size working prototypes.
During prototyping, some critical aspects are assessed:
- Performance Testing: Prototypes are extensively tested under various conditions to ascertain their reliability.
- Design Refinement: Feedback from physical models helps in identifying design flaws early on, saving time in the later stages of production.
- User Experience: Potential customers might gives feedback on usability and comfort, influencing further iterations.
โPrototypes are a revolutionary method to foresee what works in a complicated assembly.โ
In summary, the design phase, particularly through concept development and prototyping, plays an indispensable role in ensuring that Honda vehicles meet both functional and consumer expectations. The choices made here trickle down the assembly line, establishing Honda's reputation for quality and reliability while addressing challenges early in the process.
Production Planning
In the automotive industry, production planning plays a vital role in ensuring that vehicles are built efficiently and to a high standard. For Honda, a company known for its innovative engineering and quality control, effective production planning influences both output and resource management. This section delves into the core aspects of production planning, emphasizing its significance in maintaining Honda's reputation for delivering reliable vehicles.
Supply Chain Management
The foundation of production planning lies in effective supply chain management. Supply chain management refers to the method of overseeing and coordinating the full lifecycle of a product, from initial procurement through to the final delivery to customers. For Honda, managing the flow of materials is crucial for maximizing efficiency. This means ensuring that components sourced from various global suppliers arrive on time and in the right quantities.
Considerations include:
- Supplier Relationships: Fostering strong partnerships with suppliers. This helps with reliability of component delivery and ensures quality standards remain high.
- Logistical Planning: Until vehicles reach assembly lines, accurate tracking and management of shipments is vital to foresee delays or handle disruptions.
- Cost Management: Finding a balance between quality of materials and their cost recursively reflects on the final product's price.
As the global market shifts, Honda must navigate unexpected changes in the supply chain. Economic fluctuations or even natural disasters can disrupt planned production timelines. Therefore, building flexibility into the supply chain is increasingly important for Honda's adaptability.
Resource Allocation
Once supply chain components are secured, the next challenge in production planning is resource allocation. Proper allocation ensures the right amount of labor, materials, and machinery are deployed to each section of the manufacturing process.
Key factors in resource allocation include:
- Labor Deployment: Assessing workforce availability and placing talent in specialized tasks leads to better efficiency. Highly skilled workers handle intricate manufacturing processes, enhancing product quality.
- Material Usage: Allocating the correct materials minimizes waste. For instance, excessively preliminary or over-ordered parts can strain production costs.
- Machinery Maintenance: Scheduled maintenance protects against breakdown and optimizes manufacturing flow.
Resource allocation is not just practical; it also has a strategic imperative in long-term company objectives. Optimizing resource use reduces costs and maximizes returnโ aligning with Hondaโs goals for advancements and reliability. By striking an effective balance in resource allocation, Honda promotes a sustainable and proficient production line.
"Efficient production planning is essential to Honda's ongoing commitment to quality and sustainability in an ever-evolving automotive industry."
This matrix of supply chain management and resource allocation forms the backbone of Honda's efficient production planning. Each element must work in concert for Honda to continue meeting its high standards for performance and quality.
The process of assembling a Honda vehicle presents an architectural thoughtfulness, bridging design robustness with state-of-the art innovation.
Technology in Production
The integration of technology in production systems has revolutionized the automotive manufacturing landscape, and Honda exemplifies excellence in this process. Technology not only streamlines operations but also enhances precision and overall efficiency. Modern automotive production is significantly enhanced through technology, and Honda leverages this resource to maintain its competitive edge in the market.
The importance of technology in the production process encompasses various elements:
- Improved Accuracy: Technological advancements help reduce human error. This enhances the reliability of assembly processes and leads to consistently high-quality production outcomes.
- Increased Efficiency: Automation and technology reduce manufacturing times. Streamlined processes allow more vehicles to be produced in a shorter period, meeting market demands effectively.
- Cost Reduction: Advancements lead to lower operational costs. While the initial investment may be significant, the long-term benefits are substantial through savings on labor and waste throughput.
- Enhanced Data Analysis: Production technology enables better data management. This allows for monitoring of production metrics and optimization of processes based on real-time feedback.
Robotic Automation
Robotic automation plays a vital role in Honda's assembly line. The incorporation of robots has become synonymous with modern manufacturing, drastically shifting how tasks are performed. Robots can handle repetitive tasks with precision, allowing human workers to focus on more complex operations that demand higher critical thinking and dexterity.
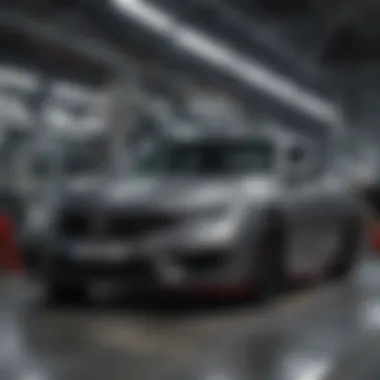
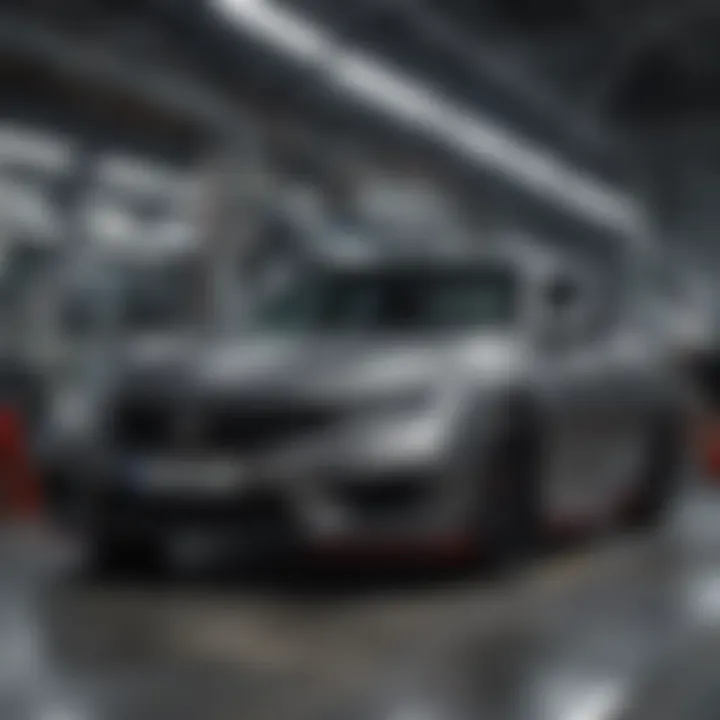
This shift also comes with several advantages:
- Consistency: Robots deliver consistent results, thereby reducing variance over time. This reliability is crucial for maintaining Hondaโs brand reputation for quality.
- Safety: Automating hazardous tasks significantly reduces the risk of accidents. Workers are less exposed to dangerous machinery or hazardous materials, establishing a safer working environment.
- Scalability: Robotic systems can be scaled according to demand. Honda can easily adjust its production capacity by reprogramming or adding robots as necessary.
Innovative Machinery
Innovative machinery is at the core of Hondaโs commitment to maintaining efficiency and productivity. From advanced stamping machines to cutting-edge assembly tools, these machines are designed to enhance operational capabilities dramatically.
Factors that make innovative machinery essential include:
- Precision Engineering: Advanced machinery enables high-precision components, ensuring the fit and function of parts in manufactured vehicles.
- Flexibility: New machinery can adapt to various production needs, allowing for mixed production runs of different models without substantial downtime.
- Energy Efficiency: Modern machines are designed with energy conservation in mind, reducing the overall carbon footprint of the manufacturing process.
โInvesting in technology is not an expense; it is a pathway to a sustainable future in automotive manufacturing.โ
Quality Control Measures
Quality control is vital in ensuring that every Honda vehicle meets the established standards of reliability and excellence. These measures not only enhance the manufacturer's reputation but also safeguard the customers' interests. In the automotive industry, where competition is intense and consumer expectations are high, Honda's dedication to quality control fosters trust among consumers and prevents significant issues post-purchase.
Inspection Protocols
Inspection protocols form a crucial component of Honda's quality control measures. The objective is to catch defects at various stages during assembly. The inspections are usually categorized based on the assembly phase:
- Incoming Inspection: Materials are assessed upon arrival at the factory. This step ensures that all parts meet specifications before progressing in the assembly process. Poor quality parts can lead to failures in the final product.
- In-process Inspection: During the assembly line, trained personnel carry out inspections regularly. Every section is evaluated for exact adherence to engineering standards and safety regulations. Qually trained employees know how to identify deviations effectively.
- Final Inspection: Once assembly is complete, each vehicle undergoes comprehensive evaluation before dispatch. This final review assesses function, aesthetics, and performanceโall critical for meeting customer expectations. Inspections here can also include test drives.
Honda also employs tools such as checklists and digital documentation. These instruments aid in maintaining records, ensuring continuity and accountability across inspections.
"Quality is never an accident; it is always the result of intelligent effort." โ John Ruskin.
Testing Procedures
Following inspection, rigorous testing procedures further enhance quality assurance. Honda implements a series of tests to validate vehicle functionality and performance, including:
- Performance Testing: Vehicles are subjected to various driving conditions to evaluate suspension, comfort, and engine performance. Data collected enables identification of any irregularities that need to be verified or rectified.
- Safety Testing: Safety attributes such as airbag deployment, brake response, and durability under impact are assessed during conformance testing. Meeting or surpassing regulations helps to ensure customer safety in diverse driving situations.
- Emission Testing: Now more than ever, being environmentally responsible is paramount. Honda administers practical tests to confirm that vehicles adhere to regulations concerning emissions, thus contributing positively to the environment.
Integrating both inspection and testing strengthens Hondaโs commitment to building reliable vehicles, translating directly to customer satisfaction and long-term loyalty.
Environmental Considerations
Environmental considerations play a crucial role in the manufacturing process of Honda vehicles. These factors not only reflect the companyโs commitment to sustainability but also affect operational efficiencies and compliance with increasingly stringent regulations globally. Incorporating environmentally friendly practices helps Honda to maintain its competitive advantage while minimizing its ecological footprint in the automotive sector.
The integration of environmentally conscious efforts starts with the design phase. Honda ensures that vehicles are built with materials that are recyclable, thus promoting a circular economy. This practice reduces waste and limits dependency on raw resources.
Sustainability Practices
Sustainability practices in Hondaโs manufacturing greatly influence its approach to production. For instance, the company has been adopting renewable energy sources, like solar and wind, to power manufacturing plants.
Here are key sustainability initiatives in Hondaโs production processes:
- Utilizing biofuels and other renewable energy sources.
- Transitioning to energy-efficient machinery.
- Implementing green building practices for construction of new facilities.
These efforts enhance not just environmental sovereignty but also foster long-term savings in energy costs. They allow Honda to by cutdown carbon emissions, ease energy consumption, and ultimately contribute to a healthier planet.
Waste Management
Effective waste management practices are integral to Hondaโs production strategy. The company implements a strategy that focuses on โreduce, reuse, recycleโ principles. Through this strategy, Honda aims to minimise waste generated during manufacturing.
Key aspects include:
- Recycling Initiatives: Standard materials like metals, plastics, and paper are systematically recycled.
- Waste Reduction: Strategies implemented across the production lines to identify areas where waste can be minimized.
- Hazardous Waste Disposal: Proper measures in handling, treatment, and disposal of hazardous materials adhere to regulatory standards.
A noteworthy effort is Honda's zero-waste initiative, where the company has targeted achieving zero landfill waste across its global operations. This proactive approach in waste management underlines Honda's aspiration to operate as an example of corporate responsibility toward the environment.
Through its commitment to sustainability and effective waste management, Honda is not just creating vehicles but also contributing to environmental preservation for future generations.
Challenges in Manufacturing
Challenges in the manufacturing process are critical to understand, especially when it comes to an intricate and reputed brand like Honda. Manufacturers face multiple obstacles that influence their production capabilities and contribute to the cost of vehicle assembly. Examining these challenges provides insight into how Honda maintains both its innovative edge and commitment to reliability. As the industry evolves, so do these difficulties, affecting production efficiency and ultimately customer satisfaction.
Global Supply Chain Issues
One prominent challenge faced by automakers is the global supply chain issues. The automotive industry relies on a complex web of suppliers sourcing materials from around the world. Natural disasters, geopolitical tensions, and health crises such as the COVID-19 pandemic have revealed vulnerabilities in this system. For example, shortages of semiconductors have significantly impacted production timelines for numerous manufacturers. Despite having a robust planning process, Honda has not been immune to these disruptions.
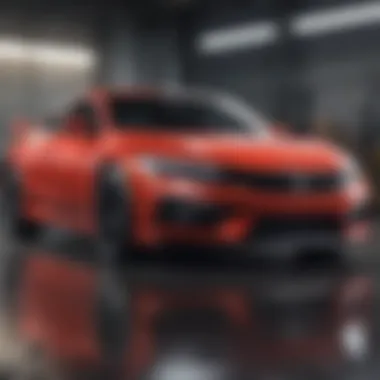
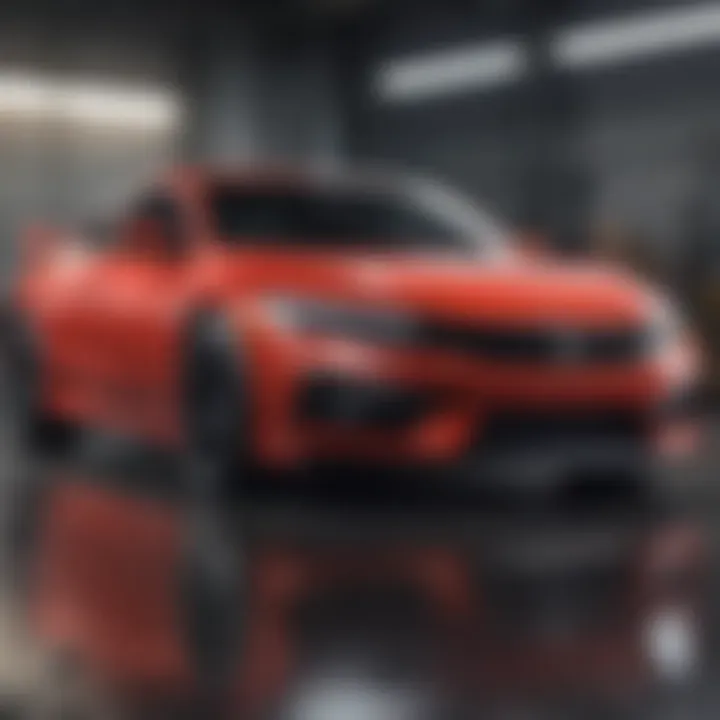
Strategies to Mitigate Supply Chain Risks
To counteract these challenges, Honda employs several strategies:
- Diversification of suppliers: Relying on multiple suppliers can reduce dependency and risk.
- Local sourcing: Establishing manufacturing plants closer to suppliers lowers transportation time and costs while improving response times.
- Technology integration: Digital tools enhance supply chain visibility, allowing Honda to make faster informed decisions.
The importance of a reliable supply chain cannot be stressed enough; it directly impacts product availability in the marketplace, which is crucial for retaining customer trust.
Labor Relations
Another challenge is the relationships between Honda and its workforce. Strong labor ties are important for maintaining productivity and ensuring high-quality standards. Yet, tensions can arise based on working conditions, wage negotiations, and the ability to meet production targets.
Factors Impacting Labor Relations
Many elements influence labor relations:
- Union negotiations: Collective bargaining can lead to strikes, halting production. Honda needs to maintain positive dialogues with unions.
- Workforce training: Providing regular training helps to uphold innovation standards, which may lead to more job satisfaction.
- Health and safety issues: Ensuring a healthy work environment is non-negotiable for attracting competent labor and minimizing risks.
To navigate these factors successfully, Honda leverages its corporate culture focused on respect for people and continuous improvement. The healthy balance between company goals and worker rights plays a role in maintaining the brand's standing in the automobile market.
Understanding these challenges is vital for appreciating the meticulous approach Honda takes in overcoming potential roadblocks in the manufacturing process.
Future Trends in Honda Manufacturing
Importance of Future Trends
As the automotive industry evolves, Honda is at the forefront of integrating future trends in manufacturing. This aspect is crucial, as it determines the company's accuracy in meeting market demands and consumer expectations. Staying ahead leads to not only greater efficiency but also the ability to maintain product relevance in an industry marked by rapid technological shifts.
This section will explore two major future trends: the electrification of vehicles and the development of autonomous vehicles. Each of these trends presents unique opportunities and challenges.
Electrification of Vehicles
The transition towards electric vehicles is fundamental in Honda's strategy. With the growing emphasis on sustainability and environmental responsibility, consumers are looking for cleaner energy options. Honda acknowledges this shift and aims to produce more electric and hybrid vehicles.
- Benefits of Electrification:
- Considerations:
- Reduced carbon emissions align with global sustainability goals.
- Lower operational costs for consumers.
- Potential government incentives to promote electric vehicle adoption.
- Infrastructure development is essential; charging stations need to be widely available.
- Battery technology still requires advancements to increase range and decrease charging times.
In response to these considerations, Honda invests in research initiatives focused on battery efficiency and energy consumption. These innovations not only enhance user experience but also push forward Hondaโs commitments to reduced ecological footprints.
Development of Autonomous Vehicles
The advancement of autonomous vehicles is another key area Honda is exploring. While fully autonomous driving may still be in the future, the significance of semi-autonomous technology is already evident.
- Innovative Features:
- Potential Challenges:
- Automated safety features like adaptive cruise control and lane-keeping assistance.
- Enhanced direction skills backed by AI computations employing real-time data.
- Regulatory landscapes must keep pace with technological advancements.
- Addressing public concerns about safety and vehicle control.
Honda is likely to work closely with governments and regulatory bodies to facilitate smoother integration of these technologies. Moreover, by emphasizing the importance of safety and resilience in its designs, Honda reassures consumers.
Innovation in manufacturing will shape the future landscape of Honda, emphasizing sustainability and safety as core values.
Ending
Understanding the complexities of assembling a Honda vehicle is crucial for recognizing the brand's commitment to quality and innovation. This conclusion synthesizes the critical elements discussed throughout the article, putting into focus the intricate process that defines Honda manufacturing. The process flows through each stage, from initial design to final assembly, emphasizing efficient methodologies and precise technologies.
Summary of Key Points
- Historical Context: Honda has a rich history that informs its current manufacturing strategies.
- Design Phase: Emotions for conceptual design align with state-of-the-art prototyping practices.
- Production Planning: Efficient supply chain management is critical for seamless production.
- Manufacturing Process: The different production phases are what enable Honda to achieve a competitive edge.
- Tech in Production: Robotic automation and innovative machinery streamline processes while maintaining high quality.
- Quality Control Measures: Consistent inspection protocols and testing ensure reliability.
- Environmental Considerations: Sustainable practices and appropriate waste management are priorities.
- Challenges: Issues like global supply chains and labor relations pose unique challenges.
- Future Trends: Honda's focus on electrification and the development of autonomous vehicles demonstrate adaptability.
The Importance of Continuous Improvement
Continuous improvement is vital. The automotive industry is evolving each day, with advancements in technology and changing consumer expectations. For Honda, this means consistently refining processes and adopting new technologies to enhance manufacturing efficiency.
Continuous improvement benefits Honda in several ways:
- Enhances vehicle quality by identifying gaps in current processes.
- Reduces waste in both production and environmental impact.
- Allows adaptive strategies to stay ahead in a competitive market.
In this dynamic industry, embracing ongoing improvements aids Honda's long-term success and ensures that customers receive vehicles that blend reliability with innovation. Honda exemplifies an approach where the pursuit of excellence continues well beyond the assembly line, ultimately ensuring that each vehicle serves both as a product and a representation of the brand's dedication to quality.
"Innovating and improving is key to maintaining excellence in today's automotive landscape."
Through these themes explored in this article, it becomes clear that understanding Honda's manufacturing processes goes beyond technical binding. It involves appreciating the values and strategies that ensure the brand remains a leader in the automotive industry.